Comment faire des dalles de pavage de vos propres mains?
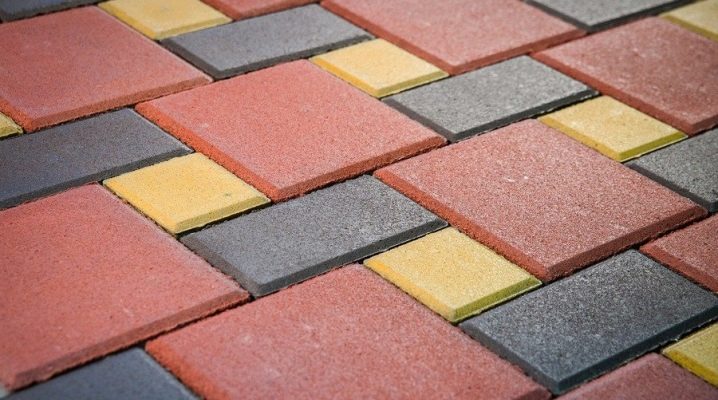
Les dalles de pavage sont un matériau populaire pour aménager des allées de jardin, des droshky à la campagne ou des terrains près des maisons privées. Vous pouvez l'acheter, et pour économiser de l'argent, vous pouvez le fabriquer vous-même. Nous vous dirons ce dont vous avez besoin pour cela.
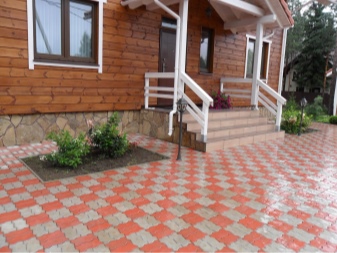
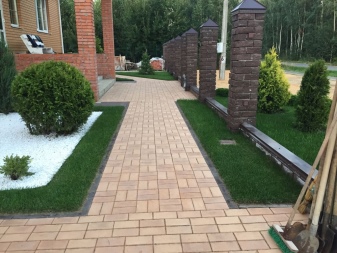
Ce qui est requis?
Lors de la production de dalles de pavage à la maison, vous aurez besoin de matières premières de haute qualité et d'équipements spéciaux.
Matériaux (modifier)
L'ingrédient principal est le ciment. Les caractéristiques techniques de la solution de travail et des pavés finis en dépendront. Lors de la fabrication de carreaux, il est recommandé de privilégier les ciments de haute qualité - au moins M400. La meilleure option est M500. Plus la valeur est élevée, plus le produit fini sera solide. Lors de l'utilisation de ciment de grade M500, les pavés auront les propriétés suivantes :
- résistance aux températures extrêmes et basses températures;
- force;
- résistance à l'eau.
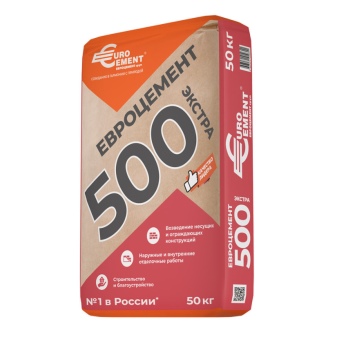
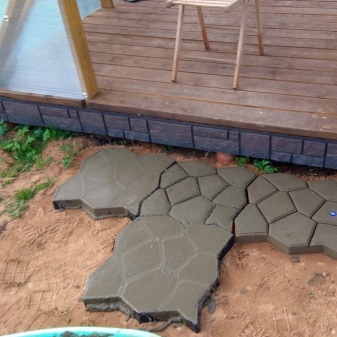
Noter! En utilisant du ciment moins cher de la marque M300, il ne sera pas possible d'économiser de l'argent, car dans ce cas, sa consommation augmentera considérablement.
Des composants supplémentaires sont également nécessaires dans la fabrication des carreaux.
- Remplissage grossier. Il peut s'agir de pierre concassée, de cailloux ou de scories - leurs tailles doivent être comprises entre 3 et 5 mm. Le mastic augmente la densité des carreaux et leur résistance à l'abrasion. Parfois, l'argile expansée est utilisée comme scellant. Cependant, son utilisation est indésirable, car en raison de la porosité élevée de ce matériau, les carreaux peuvent éclater au gel.
- Remplissage à grain fin - sable de rivière tamisé (sans impuretés mécaniques et sans argile).
- L'eau. Mieux vaut utiliser de l'eau potable à température ambiante ou un liquide distillé.
- Plastifiant. Dans les quincailleries, ces additifs sont vendus sous forme de poudre ou de liquide. En raison de l'ajout d'un plastifiant à la solution, la consommation de ciment et de liquide diminuera et la densité de la solution augmentera. Les additifs améliorent non seulement les caractéristiques techniques du pavé (augmentent la résistance mécanique, la résistance au gel et la résistance à l'humidité), mais facilitent également grandement le processus de mélange de la masse de ciment.
- Teintures. Les carreaux de couleur aideront à décorer avec goût les chemins ou les plates-formes ou à s'agencer au bâtiment construit. Pour donner de l'ombre, des pigments en solution spéciaux ont été créés. Selon la quantité de peinture ajoutée, la composition peut être des tons pâles clairs ou, au contraire, brillants. Les colorants sont disponibles sous forme de poudre. Lors de leur utilisation, une bétonnière doit être utilisée pour préparer la solution de travail. Mélanger les ingrédients à la main ne répartira pas la peinture uniformément.
- Lubrification. Il est nécessaire de faciliter le démoulage des carreaux. Vous pouvez acheter un lubrifiant spécial, par exemple "Emulsol", "Lirossin" ou utiliser de l'huile moteur ou de l'huile végétale, une solution savonneuse.
Les constructeurs recommandent d'ajouter des durcisseurs à la solution - ce sont des additifs spéciaux qui augmentent le processus de durcissement et réduisent le risque de fissuration des pavés.
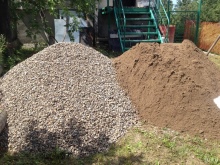
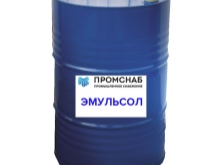
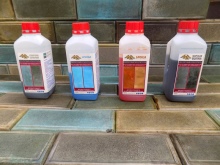
Équipement
Pour fabriquer des carreaux de vos propres mains, vous avez besoin d'une bétonnière ou d'un perforateur avec une buse de mélangeur spéciale. Le choix de telle ou telle unité dépend de l'ampleur des travaux. Dans la production de pavés, vous ne pouvez pas vous passer d'une table vibrante.Une telle installation est nécessaire pour compacter la solution de béton, éliminer les bulles d'air et répartir uniformément la masse dans le coffrage.
La vibration rendra le carreau plus durable et sa face plus lisse.
Pour fabriquer des pavés à la maison, vous ne devez pas acheter une unité de production - vous pouvez fabriquer vous-même une table vibrante à partir d'une machine à laver ancienne mais en bon état de fonctionnement ou à partir d'un broyeur électrique (ou d'un autre équipement doté d'un moteur de puissance appropriée).
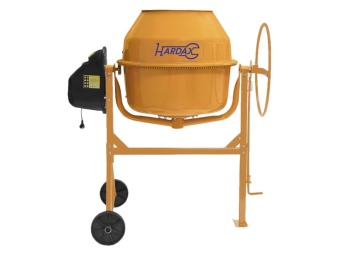
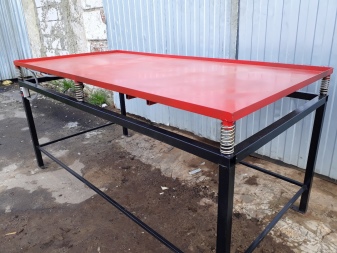
Pour mélanger le mortier de béton, vous ne pouvez pas non plus vous passer de :
- conteneurs (bassin ou grand seau);
- verres avec des marques (pour des mesures précises du colorant);
- truelle;
- pinceau pour lubrifier les moules;
- formes.
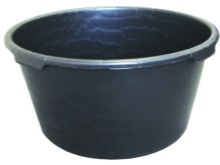
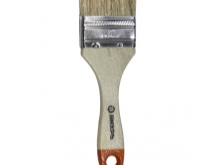
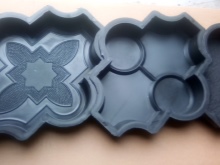
Les moules de coulée diffèrent par les matériaux de fabrication, la configuration et le coût. En vente, il existe des produits en plastique, en caoutchouc et en polyuréthane. Les moules en caoutchouc sont parmi les plus durables, résistent jusqu'à 500 cycles de coulée. Les plastiques sont moins fiables, ils peuvent supporter environ 250 cycles et le polyuréthane - 100. Parmi les formes, les produits les plus demandés et les plus populaires sont en plastique. Ils se distinguent par leur résistance à l'usure, répètent bien le relief, sont durables et ne se déforment donc pas lorsqu'ils sont remplis de mortier.
Pour économiser sur l'achat de formulaires prêts à l'emploi, leur production maison aidera. À ces fins, des blocs de bois, du contreplaqué résistant à l'humidité ou des tôles minces conviennent. Certains artisans préfèrent couler du béton dans des plateaux ménagers. Pour la production de carreaux, de nombreuses formes sont nécessaires (au moins 20-30). Avec un petit nombre d'entre eux, le processus de fabrication prendra beaucoup de temps.
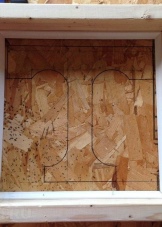
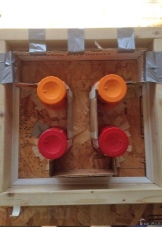
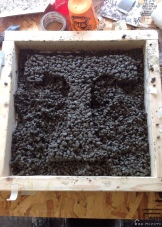
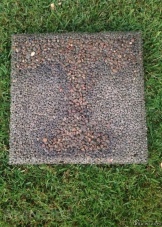
Comment préparer la solution ?
Pour obtenir des carreaux de haute qualité lors de la préparation de la masse de béton, les proportions de tous les composants et la technologie de fabrication doivent être respectées.
Pour trouver une solution, vous aurez besoin de :
- charge (pierre concassée, cailloux) - 38 kg;
- sable - 18 kg;
- ciment - 17 kg (marque M500);
- plastifiant - selon les instructions;
- eau - 9 litres.
- couleur - en fonction de la couleur souhaitée 3-5% en poids du ciment.
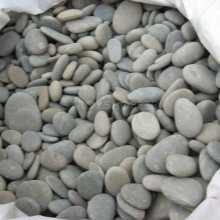
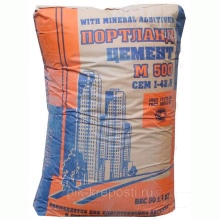
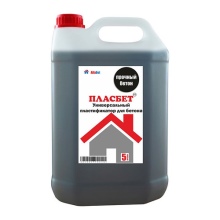
Le mélange comprend plusieurs étapes. Considérons-les étape par étape :
- tout le volume de sable, 2/3 de pierre concassée et de ciment doit être versé dans la bétonnière, allumez l'appareil pour mélanger les composants secs;
- eau, un plastifiant doit être introduit dans le tambour (la substance est préalablement diluée dans de l'eau tiède jusqu'à dissolution complète) et les composants doivent être mélangés pendant 1 minute;
- Ensuite, vous devez remplir le reste de la charge, colorer et mélanger pendant 1-2 minutes.
Il est permis de mélanger la masse de béton dans les 3 heures. Par temps particulièrement chaud, l'humidité s'évapore rapidement de la solution, provoquant l'épaississement de la solution. Il est impossible d'ajouter de nouvelles portions d'eau pour liquéfier la masse - dans ce cas, les caractéristiques techniques du béton se détérioreront.
Pour que la solution n'ait pas le temps de s'épaissir, il est recommandé de mélanger en petits volumes (la consommation optimale du mélange préparé est dans les 20 minutes).
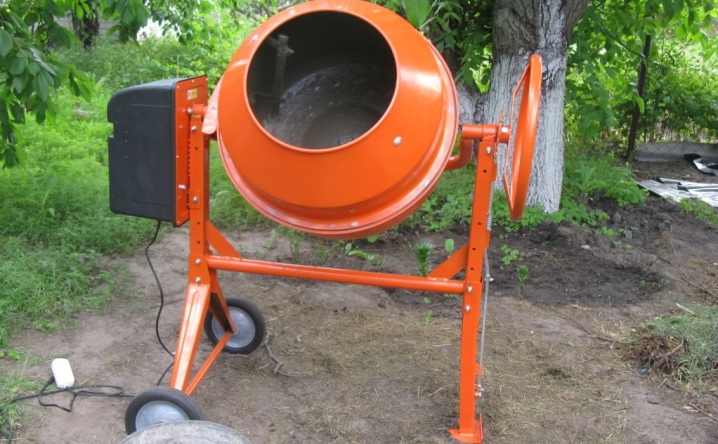
Lubrification du moule
Avant de commencer les travaux, les coffrages doivent être nettoyés - ils ne doivent pas contenir de petits débris et autres contaminants, car tout cela peut gâcher l'esthétique du matériau de parement fini. Une solution de savon ou tout détergent à vaisselle de type gel aidera à éliminer la graisse.
Il est impossible de lubrifier correctement les coffrages à l'avance - uniquement avant de couler le mortier de ciment. Vous devez répartir le mélange en une fine couche sur toute la surface du moule afin qu'il n'y ait pas de zones non traitées. À ces fins, un pinceau, une éponge ou un flacon pulvérisateur convient. Lors de la lubrification, il est nécessaire de s'assurer qu'aucun poil de brosse ne reste à la surface du moule.
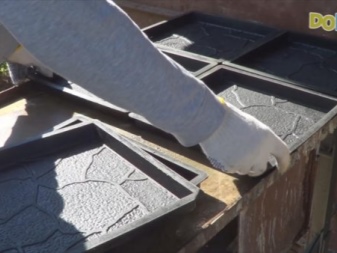
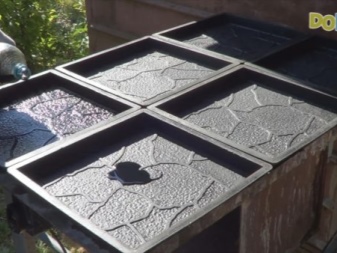
Comment verser la masse de ciment?
La prochaine étape est le moulage. Il est préférable de remplir les coffrages lubrifiés avec du mortier de ciment à la main à l'aide d'une spatule. Pour réaliser soi-même les carreaux colorés et en même temps économiser sur la couleur, il est recommandé de verser d'abord la masse colorée (environ 25% du volume du moule), puis la grise sans colorant.Dans ce cas, il est nécessaire de maintenir un intervalle entre les remplissages de 20 minutes. Sinon, la couche peinte et grise n'adhérera pas fermement et pourrait se détacher.

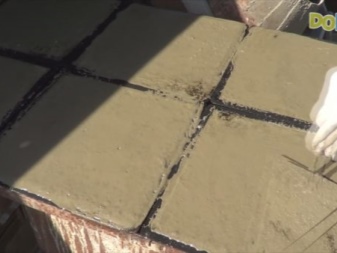
Pressage
Après avoir coulé, le moule doit être secoué légèrement et placé sur une table vibrante. Le temps de pressage est de 2 à 5 minutes. Parfois, une fois compactée, la solution "s'assoit". Dans ce cas, il est nécessaire de rapporter le mortier de ciment aux bords du moule.
Lors du pressage, les bulles d'air sont éliminées de la masse et tendent vers la surface, formant une mousse blanche. Son affaissement indique qu'il est temps de terminer le scellement. Ne compactez pas la masse de ciment trop longtemps, sinon elle exfoliera.
Si des pavés bicolores sont fabriqués, le mortier doit être compacté après avoir coulé chaque couche. La deuxième couche durcit en 2-3 minutes (dans ce cas, l'apparition de mousse est facultative).
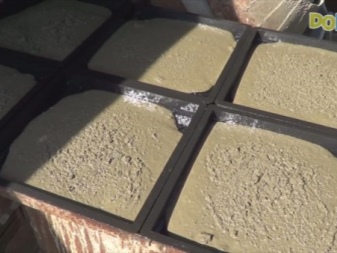
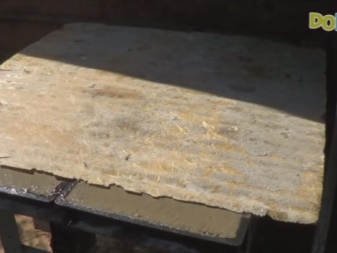
Séchage
Les coffrages avec du mortier compacté doivent être placés sur des claies pour le séchage, au cours desquels l'excès d'humidité s'évapore de la masse de ciment. Le temps de séchage dépend de la température et est de 2-3 jours.
Les racks doivent être installés dans un endroit sec et bien aéré, bien protégé des rayons directs du soleil. Lorsqu'ils sont exposés à une lumière intense, les pavés se fissurent.
Pour réduire le taux d'évaporation de l'humidité, il est recommandé de mettre une pellicule plastique sur les moules.
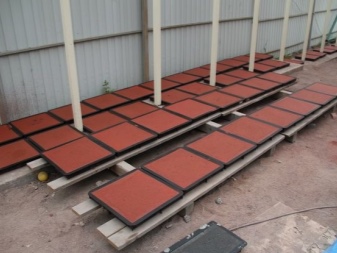
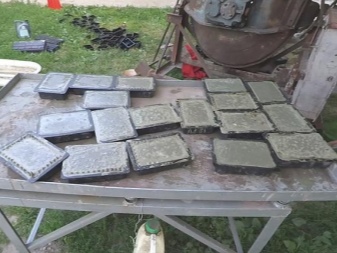
Démoulage
Ce terme désigne le démoulage des pavés. Immerger le moule coulé dans de l'eau chaude (au moins 60 degrés) facilitera le retrait du carreau. Lorsqu'elle est exposée à la chaleur, la forme se dilatera, ce qui permettra de retirer le produit sans éclats, fissures et autres défauts.
Après avoir retiré les pavés, ils doivent rester encore 7 jours sur la grille. Après cela, les produits peuvent être empilés sur des palettes et séchés pendant 30 jours supplémentaires. Sinon, les pavés n'obtiendront pas la résistance requise - ils s'effondreront et se briseront lors de la pose.
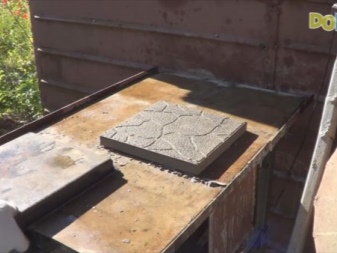
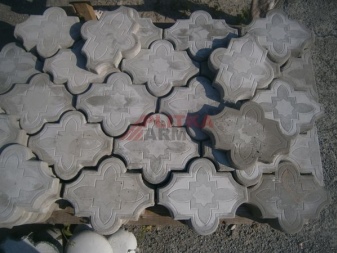
Teinture
La teinture de surface aidera à colorer les pavés. Ils y ont recours si aucune couleur n'a été utilisée lors du mélange du mortier de ciment. Ou les dalles de pavage deviennent ternes pendant le fonctionnement. L'utilisation de peintures spéciales est un moyen rapide et peu coûteux d'ajouter des peintures à votre aménagement paysager. De plus, en raison des taches, une coque est créée qui protège les pavés des influences météorologiques négatives (changements de température, précipitations, humidité élevée). Grâce à cette caractéristique, la durée de vie de la tuile est augmentée.
Il n'y a qu'un seul inconvénient à la coloration - la nécessité d'un renouvellement périodique de la couleur. Dans les endroits infranchissables, les travaux sont effectués 1 fois en 10 ans, et là où le trafic est important, il faudra peindre les carreaux 1 fois en 2-3 ans.
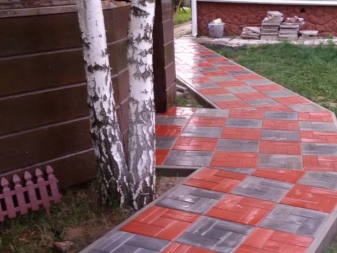
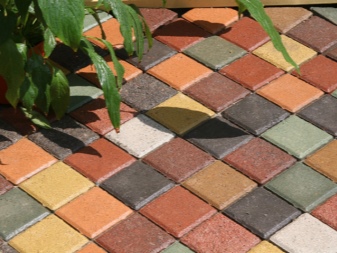
Plusieurs compositions conviennent à la peinture.
- Caoutchouc. Leurs caractéristiques sont: haute élasticité et résistance à l'eau. Les peintures à base de caoutchouc créent un revêtement antidérapant à la surface du revêtement, résistant aux basses et hautes températures, aux UV du soleil. La peinture en caoutchouc ne craque pas et conserve longtemps l'éclat des couleurs. Les formulations sont non toxiques.
- Alkyde. Ils créent un revêtement décoratif durable sur la surface qui protège de manière fiable les pavés de l'abrasion mécanique. L'inconvénient de telles formulations est une odeur désagréable qui met longtemps à disparaître.
- Polyuréthane. De telles compositions peuvent être appliquées même en hiver.
Les peintures polyuréthane sèchent rapidement, n'émettent pas d'odeur chimique forte, mais se fanent rapidement au soleil et se fanent.
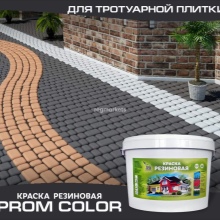
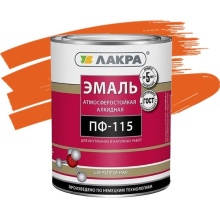
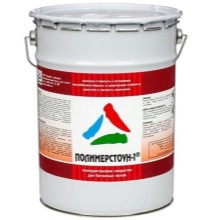
La peinture doit être effectuée par temps sec et calme. La plupart des formulations sont autorisées à être utilisées à des températures supérieures à +10 degrés (les conditions d'utilisation peuvent être trouvées dans les instructions du fabricant).
Il est recommandé de traiter les pavés au mordant acide avant de peindre. - il rendra le matériau poreux, de sorte que la peinture pénètrera rapidement et facilement dans ses couches profondes.Les travaux préparatoires obligatoires comprennent le dégraissage des dalles de pavage, l'élimination des débris et de la saleté de sa surface.
Un rouleau à peinture ou un pinceau convient à la peinture. Toute peinture ne doit pas être appliquée avec une touche légère, mais frottée sur les pavés. Les carreaux doivent être peints au moins 2-3 fois. Dans ce cas, il est nécessaire d'appliquer la couche suivante seulement après que la précédente soit complètement sèche. Le temps de séchage dépend des conditions de température et d'humidité.
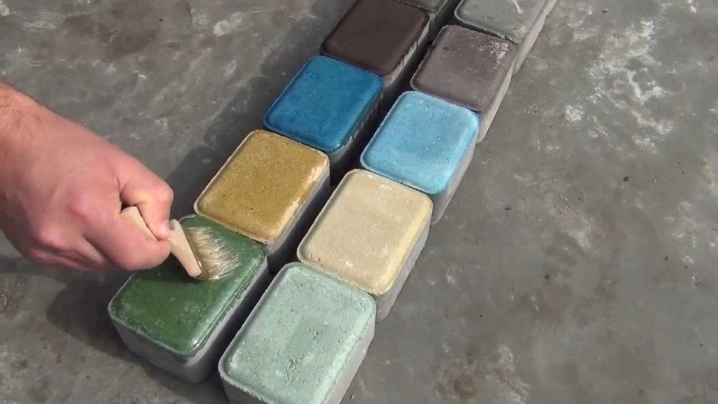
Astuces utiles
Les dalles de pavage esthétiques, fabriquées à la main, pourraient bientôt commencer à s'effondrer. Il existe de nombreuses raisons à ce phénomène, mais la plupart d'entre elles sont un désir d'économiser de l'argent et une violation des règles de la technologie.
Voici quelques recommandations utiles, dont le respect aidera à obtenir des pavés de haute qualité et visuellement attrayants.
- L'utilisation de sable de mauvaise qualité. Une évaluation visuelle des granulats fins ne suffit pas. On trouve souvent de petits coquillages dans le sable. Lorsqu'ils sont pressés, ils se déposent sur la face du carreau et gâchent son motif. Pour éviter que cela ne se produise, même à première vue, du sable de haute qualité doit être tamisé.
- Non-respect des proportions d'eau. "Pâte collante" - la consistance optimale du coulis de ciment. Une application excessive d'eau entraînera une fragilité accrue du matériau, insuffisante - à la formation de pores sur le visage.
- L'utilisation d'huiles usagées pour la lubrification des moules. Pour éviter que la face extérieure ne soit endommagée par des points noirs, vous devez utiliser des produits spéciaux.
- Séchage de produits déformés par temps chaud. Pour éviter que les carreaux ne se fissurent à cause de l'évaporation rapide de l'humidité, il est recommandé de mouiller régulièrement les produits.
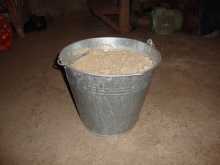
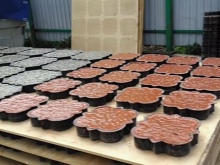
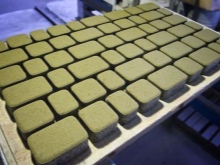
Les dalles de pavage doivent être réalisées dans une pièce sans poussière et en combinaison, car la poussière réduit les caractéristiques techniques du matériau fini. Sous réserve des proportions de la masse de ciment, de la technologie de son mélange et des recommandations utiles, vous n'aurez aucun problème avec la production indépendante de dalles de pavage.
Pour plus d'informations sur la fabrication de dalles de pavage de vos propres mains, voir la vidéo suivante.
Le commentaire a été envoyé avec succès.